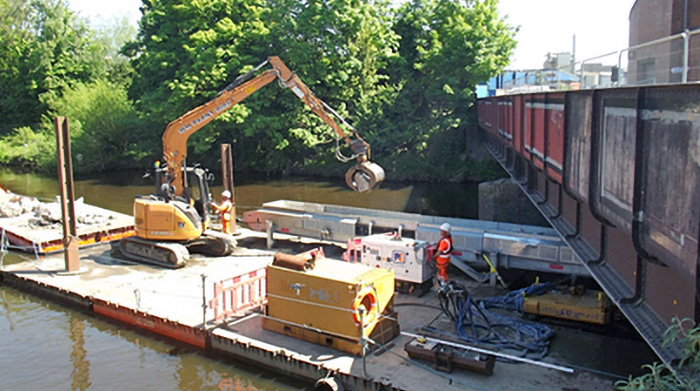
East Coast Road Scour Protection
East Coast Road Bridge in Sheffield is a two-span road bridge with a maintenance liability assigned to Network Rail by a Victorian access covenant. The bridge features a 3-tonne weight restriction. Suttle Projects were contracted to carry out a rock armour installation to a central masonry pier, beneath a low headroom bridge deck.
There were challenges to overcome with this scheme. Scour protection projects often do not merit detailed soils investigations, precontract. An initial plan to dewater the structure with sheet piles was set aside by the discovery of fairly shallow bedrock to the structure.
In 2015 Suttle Projects developed a remote-control underwater excavator, branded The Little Mermaid. This is for use in situations where we have to excavate in live river channels, in confined and sometimes low headroom environments. We planned to deploy the Mermaid machine on the riverbed at Sheffield and complete the scour installation within a silt curtain confined environment, digging and placing rock. The final obstacle proved to relate to the surrounding industry.
The bridge leads to an historic industrial area featuring heavy steel and iron-based engineering. On initial excavation it became apparent that the area upstream, downstream and beneath the bridge were strewn with wire and metal obstacles that had been cast into the river by previous generations, working within the neighbouring factories. This metal even included a handgun, that was duly reported to local police. This made tracking of our excavator on the riverbed untenable, both in terms of entanglement and likely hydraulic leaks from metal punctures. We re-thought. Instead we used a recessed pontoon to create an ultra-low headroom floating digging device, incorporating the Mermaid beneath the bridge.
We then further improved by overcoming the materials handling problem of getting rock beneath the structure, by mounting a hydraulically powered conveyor on the floating pontoon. With a hopper that could be loaded outside the bridge deck envelope, this combination promptly and efficiently solved a complex problem relating to the nature of the work and the surrounding environment. The latter stages demonstrated an unexpected capability of working nationally within the context of the COVID 19 epidemic.
Good value, high quality materials and service